Recambios da motoniveladora XCMG Liugong do eixe do motor
Eixo condutor
Debido a que hai moitos tipos de pezas de recambio, non podemos mostralas todas no sitio web. Por favor, póñase en contacto connosco para cuestións específicas.
Vantaxe
1. Ofrecémosche produtos orixinais e posventa
2. Do fabricante ao cliente directamente, aforrando o seu custo
3. Stock estable para pezas normais
4. En tempo de entrega, cun custo de envío competitivo
5. Profesional e puntual despois do servizo
Embalaxe
Caixas de cartón, ou segundo a solicitude dos clientes.
descrición
O eixe motriz é unha das pezas fundamentais da parte motriz do chasis da maquinaria de construción. Está sometido a flexión complexa, cargas de torsión e grandes cargas de impacto durante o uso, o que require que o semi-eixe teña unha alta resistencia á fatiga, dureza e boa resistencia ao desgaste. A vida útil do semi-eixe non só se ve afectada polo plan e a selección do material na fase de deseño do proceso do produto, senón que tamén son moi importantes o proceso de produción de forxa e o control de calidade dos forxados.
Análise da calidade dos procesos e medidas de control no proceso produtivo
1 Proceso de corte
A calidade do corte afectará á calidade dos seguintes brancos de forxa libre e mesmo á forxa de matrices. Os principais defectos no proceso de baleirado son os seguintes.
1) A lonxitude está fóra de tolerancia. A lonxitude de corte é demasiado longa ou demasiado curta, demasiado longa pode facer que as forxas sexan excesivamente positivas en tamaño e materiais de refugallo, e demasiado curta pode provocar que as forxas non estean satisfeitas ou sexan de pequeno tamaño. O motivo pode ser que o deflector de posicionamento estea configurado incorrectamente ou que o deflector de posicionamento estea solto ou inexacto durante o proceso de baleirado.
2) A pendente da cara final é grande. Unha gran pendente da superficie final significa que a inclinación da superficie final do branco con respecto ao eixe lonxitudinal supera o valor permitido especificado. Cando a inclinación da cara final é demasiado grande, pódense formar dobras durante o proceso de forxa. O motivo pode ser que a barra non estea suxeita durante o corte, ou a punta do dente da serra de cinta está desgastada anormalmente, ou a tensión da folla da serra de cinta é demasiado pequena, o brazo guía da máquina de serra de cinta non está no mesmo liña horizontal, etc.
3) Rebaba na cara final. Ao serrar o material da barra, as rebabas adoitan aparecer na rotura final. É probable que os brancos con rebabas causen sobrequecemento local e queimaduras excesivas cando se quentan, e son fáciles de dobrar e rachar durante a forxa. Unha razón é que a folla de serra está envellecida, ou os dentes da serra están desgastados, non están o suficientemente afiados ou a folla de serra ten os dentes rotos; a segunda é que a velocidade da liña da folla de serra non está configurada correctamente. Xeralmente, a nova folla de serra pode ser máis rápida e a antiga máis lenta.
4) Gretas na cara final. Cando a dureza do material é desigual e a segregación do material é grave, é fácil producir fisuras na cara final. Para os brancos con fendas finais, as fendas expandiranse aínda máis durante a forxa.
Co fin de garantir a calidade do corte, tomáronse as seguintes medidas de control preventivo durante o proceso de produción: antes do corte, verifique a marca do material, a especificación, a cantidade e o número do forno de fundición (lote) de acordo coa normativa do proceso e as tarxetas de proceso. . E comprobe a calidade superficial das barras de aceiro redondas; o corte realízase en lotes segundo o número de forxa, a marca do material, a especificación e o número de forno de fusión (lote), e o número de espazos en branco indícase na tarxeta de seguimento de circulación para evitar a mestura de materiais estraños; Ao cortar o material, o sistema de "primeira inspección", "autoinspección" e "inspección de patrulla" debe implementarse de forma estrita. A tolerancia dimensional, a inclinación final e a rebaba final do espazo en branco deben inspeccionarse con frecuencia segundo os requisitos do proceso, e a inspección está cualificada e o estado do produto está marcado. A orde pódese cambiar despois; durante o proceso de corte, se se detecta que os espazos en branco presentan dobras, cicatrices, fendas finais e outros defectos visibles, deberase informar ao inspector ou técnicos para a súa eliminación a tempo; O lugar de corte debe manterse limpo, con diferentes calidades de materiais e número de forno de fundición (lote), especificacións e dimensións deben colocarse por separado e claramente marcados para evitar mesturas. Se é necesaria a substitución de material, débense seguir rigorosamente os procedementos de aprobación para a substitución de material e os materiais só se poden descargar despois da aprobación.
2 Proceso de calefacción.
O proceso de produción de semi-eixe quéntase por dous lumes, o tacho de forxa libre quéntase por un forno de gas e a forxa de matriz quéntase por un forno eléctrico de indución, polo que o control preventivo da secuencia de quecemento é máis complicado e máis difícil; Para garantir a calidade da calefacción, formulamos as seguintes especificacións de calidade:
Cando se quenta a cociña de gas, non se permite cargar directamente o material na zona de alta temperatura e non se permite pulverizar a chama directamente sobre a superficie do espazo en branco; ao quentar no forno eléctrico, a superficie do branco non debe estar contaminada con aceite. As especificacións de calefacción implementaranse segundo os requisitos das correspondentes normativas de proceso de forxa, e a temperatura de quecemento de 5-10 pezas en branco deberase verificar completamente antes da quenda para demostrar que os parámetros de calefacción son estables e fiables. O tocho non se pode falsificar a tempo debido a problemas de equipamento e ferramentas. Pódese procesar arrefriando ou fóra do forno. O tocho empuxado debe marcarse e almacenarse por separado; o tacho pódese quentar repetidamente, pero o número de quecemento non pode exceder 3 veces. A temperatura do material cando se quenta o espazo en branco debe controlarse en tempo real ou regularmente cun termómetro infravermello, e debe facerse o rexistro de quecemento.
3 Proceso de elaboración de billetes.
Os defectos comúns durante a fabricación do tocho inclúen un diámetro ou lonxitude excesivos da varilla intermedia, marcas de martelo na superficie e transicións de pasos deficientes. Se o diámetro da varilla é demasiado positivo, será difícil metelo na cavidade durante a forxa. Se a varilla é pequena negativa, a coaxialidade da forxa pode ser demasiado pobre debido á gran brecha da varilla durante a forxa; É posible que sexan posibles marcas de martelo na superficie e unha transición deficiente do paso. Levar a fosas ou dobras na superficie da forxa final.
4 Proceso de forxa e recorte.
Os principais defectos no proceso de forxa de matrices de semi-eixe inclúen o pregamento, o recheo insuficiente, a depresión (non golpear), o desalineamento, etc.
1) Dobrar. O pregamento do semi-eixe é común na cara final da brida, ou no filete de paso ou no medio da brida, e xeralmente ten forma de arco ou mesmo semicircular. A formación do pregamento está relacionada coa calidade do branco ou intermedio, o deseño, fabricación e lubricación do molde, a suxeición do molde e do martelo e a operación real de forxa. O pregamento xeralmente pódese observar a simple vista cando a forxa está nun estado quente, pero normalmente pode pasar a inspección de partículas magnéticas na fase posterior.
2) Cheo parcialmente de insatisfacción. A insatisfacción parcial das forxas semi-eixe prodúcese principalmente nas esquinas redondas exteriores da varilla ou brida, o que se manifesta porque as esquinas redondeadas son demasiado grandes ou o tamaño non cumpre os requisitos. A insatisfacción levará a unha redución da sobremesa de mecanizado da forxa e, cando sexa grave, procederase ao despezamento da transformación. Os motivos da insatisfacción poden ser: o deseño do tocho intermedio ou en branco non é razoable, o seu diámetro ou lonxitude non está cualificado; a temperatura de forxa é baixa e a fluidez do metal é pobre; a lubricación da matriz de forxa é insuficiente; a acumulación de escamas de óxido na cavidade da matriz, etc.
3) Deslocalización. O desalineamento é o desprazamento da metade superior da forxa en relación á metade inferior ao longo da superficie de separación. A colocación incorrecta afectará o posicionamento do mecanizado, dando lugar a unha asignación de mecanizado local insuficiente. As razóns poden ser: o espazo entre a cabeza do martelo e o carril guía é demasiado grande; o deseño da brecha de bloqueo da matriz de forxa non é razoable; a instalación do molde non é boa.
5 Proceso de corte.
O principal defecto de calidade no proceso de recorte é o flash residual grande ou irregular. Un flash residual grande ou irregular pode afectar o posicionamento e a suxeición do mecanizado. Ademais do aumento da asignación de mecanizado local, tamén provocará a desviación do mecanizado e mesmo pode provocar cortes por corte intermitente. O motivo pode ser: o punzón da matriz de recorte, a brecha da matriz non está deseñada correctamente ou a matriz está desgastada e envellecida
Co fin de evitar os defectos mencionados anteriormente e garantir a calidade das pezas forxadas, formulamos e adoptamos unha serie de medidas de prevención e control: determinar o tamaño adecuado de branco ou intermedio mediante a revisión do deseño e a verificación do proceso; na fase de deseño e verificación do molde, agás no molde convencional. Ademais do deseño da cavidade, da ponte e do silo, prestouse especial atención aos filetes de paso e a bloquear ocos para evitar que se dobra e se desplacen mal, un estrito control de calidade do proceso de corte, quecemento e forxa libre de tochos, e céntrase na superficie oblicua do tocho. Graos e rebabas na cara final, transición escalonada do tocho intermedio, lonxitude da varilla e temperatura do material.
O noso almacén 1
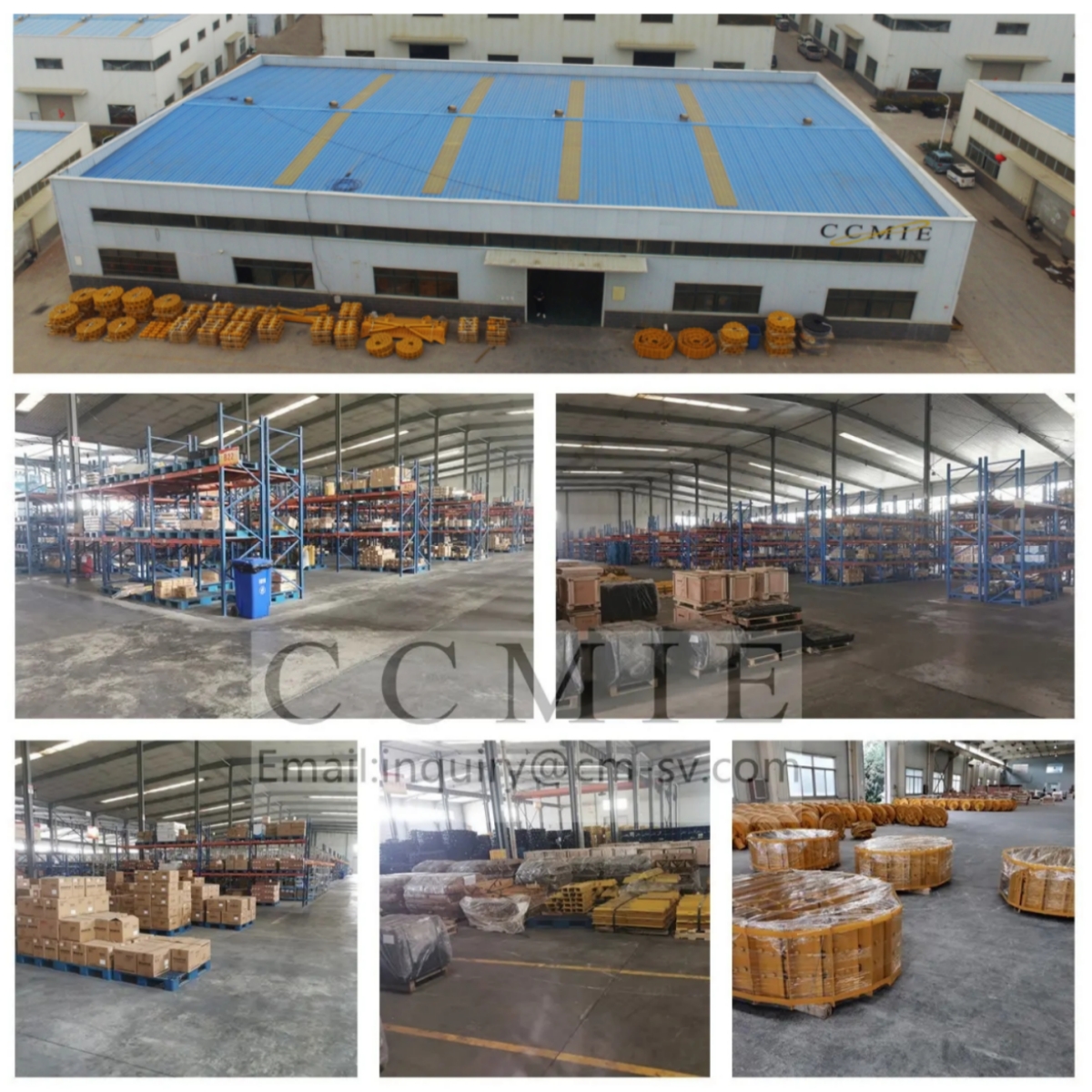
Empaque e envíe

- Ascensor aéreo
- Camión volquete de China
- Reciclador en frío
- Forro de trituradora de cono
- Elevador lateral de contedores
- Parte de Bulldozer Dadi
- Accesorio barredora para carretilla elevadora
- Pezas para Bulldozer Hbxg
- Pezas do motor Howo
- Bomba hidráulica para excavadora Hyundai
- Recambios para Bulldozer Komatsu
- Eixo de engrenaxe da excavadora Komatsu
- Bomba hidráulica para excavadora Komatsu PC300-7
- Pezas de Bulldozer Liugong
- Recambios para bombas de formigón Sany
- Recambios para escavadoras Sany
- Pezas do motor Shacman
- Eixo de embrague de bulldozer Shantui
- Pasador de eixe de conexión para bulldozer Shantui
- Shantui Bulldozer Control Eixo Flexible
- Shantui Bulldozer Eixo Flexible
- Kit de reparación de cilindro de elevación de bulldozer Shantui
- Recambios para Bulldozer Shantui
- Eixo do carrete de bulldozer Shantui
- Shantui Bulldozer Eixo de marcha atrás
- Recambios para Bulldozer Shantui
- Shantui Bulldozer Winch Eixo de transmisión
- Parafuso dozer Shantui
- Rodillo frontal Shantui Dozer
- Kit de reparación de cilindros de inclinación dozer Shantui
- Engrenaxe cónica Shantui SD16
- Forro de freo Shantui SD16
- Montaxe de porta Shantui Sd16
- Shantui Sd16 O-Ring
- Rodillo de oruga Shantui Sd16
- Manga de rodamento Shantui SD22
- Disco de fricción Shantui SD22
- Rodillo de oruga Shantui Sd32
- Pezas do motor Sinotruk
- Camión de remolque
- Recambios para Bulldozer Xcmg
- Recambios para Bulldozer Xcmg
- Bloqueo hidráulico Xcmg
- Transmisión Xcmg
- Pezas do motor Yuchai